With Descartes' Netsuite WMS Integration Incipio Automated Order Fulfillment
With expansive growth in order volume, Incipio needed a hyper-efficient, integrated warehouse management solution. Outdated, paper-based processes led to inaccurate and delayed order fulfillment and it was challenging to meet increased demand. Descartes Ozlink™ for Netsuite automated and streamlined Incipio’s order fulfillment processes to increase productivity, reduce costs, improve accuracy, and optimize inventory control.
Challenge: Supporting Expansive Growth
The rise of mobile, technology-driven lifestyles drastically increased demand for Incipio’s products. In a few short years, order volume grew from 50k to 250k daily units and placed substantial pressure on logistics operations.
Incipio’s inefficient paper practices could not keep pace with increasingly complex shipping and warehouse requirements. “We had to write everything down—weight, number of pieces, quantity, pallet dimensions, etc.—and take the hand-written documentation to the office to print labels. No one in the warehouse could print a label,” said Martin Kudo, WMS IT Manager, Incipio, “It was extremely backwards and inefficient.”
We’ve seen an enormous improvement in fulfillment efficiency—at least 80%. With instant order verification, wireless barcode scanning has dramatically improved our picking, packing, and shipping productivity. And we can create labels automatically without having to shuffle hand-written documents from the warehouse to the office. Descartes OzLink has been a total lifesaver.
-Martin Kudo, WMS IT Manager, Incipio
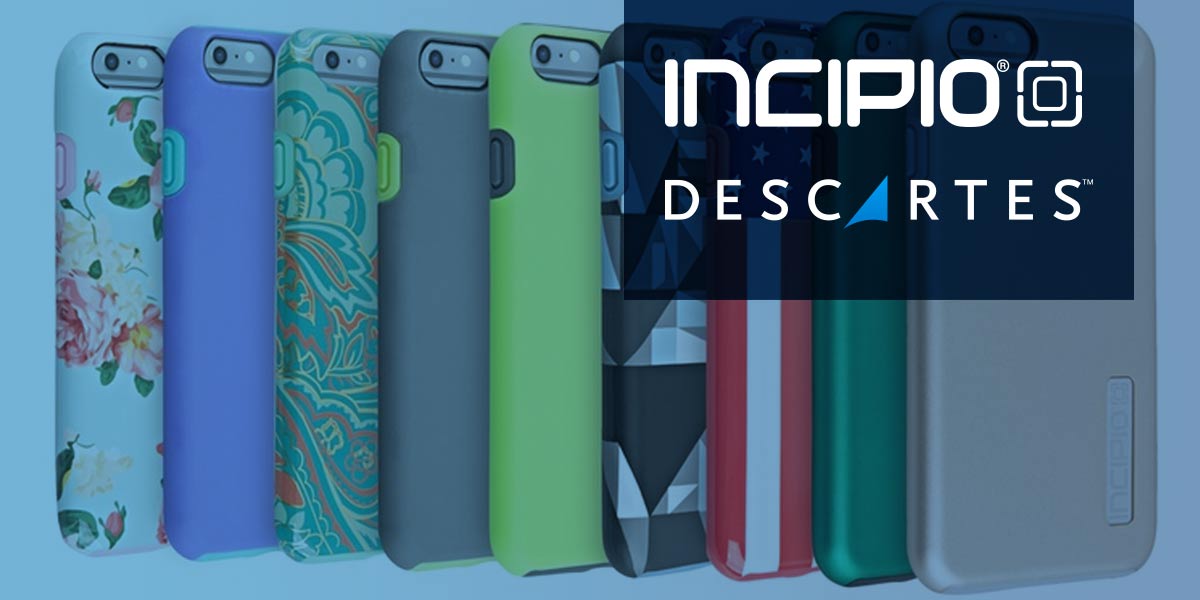
Solution: Automated Fulfillment Streamlines Processes
Recognizing their need to adopt modern solutions for their warehouse operations, Incipio deployed Descartes OzLink for NetSuite to automate shipping processes with key carriers at its Irvine, California location. Implementation of Advanced shipping Notice (ASN) automation for large retail partners and bar code scanning followed. With the acquisition of a mobile-accessories provider and its warehouse, Incipio moved some of its fulfillment to Nashville, Tennessee to centralize distribution.
Descartes OzLink is a key component of these new operations. By integrating seamlessly with NetSuite and carrier applications, Descartes OzLink has streamlined Incipio’s pick, pack, and ship processes. Using mobile barcode scanners, warehouse employees pick single and multiple orders more efficiently and accurately. The Descartes system also makes it easier to verify orders during the process, including ASNs.
The Results
- Greater Accuracy - Order validation with barcode scanning reduced picking errors dramatically. With automated labels and packing lists with seamless integration between Descartes OzLink, NetSuite, and various carrier applications, Incipio increased order accuracy.
- Increased Efficiency - Implementing barcode scanning into the warehouse has streamlined the order fulfillment process to handle routine and high volumes efficiently. Multiple order picking, automated labels, and the elimination of paper-based processes boosted productivity.
- Tighter Inventory Control - Wireless, mobile barcode scanners enable better inventory visibility and support daily cycle counts. With Descartes OzLink, Incipio no longer needs to shut down warehouse operations for a full day to perform physical inventory counts.
- Decreased Costs - Descartes OzLink has helped Incipio save money by eliminating inefficient, error-prone manual processes. The solution reduced warehouse costs, provided better inventory control, and decreased labor costs.
Looking to meet with a solution expert?