While pursuit of the “perfect order” will always be a daily challenge, today’s global marketplace means that companies are under increasing pressure to quickly fulfill product orders across complex networks – and do so holding as little inventory as possible and not make costly errors that might drive business away. This has led to a rise in the use of cross-docking, and the need for an automated solution that ensures the supply chain does not sacrifice accuracy for speed.
What is Cross-Docking?
Cross-docking is commonly defined as the process of unloading products or materials directly from one transport vehicle to another without the intermediary step of being placed in a warehouse or storage facility between transit stops. Cross-docking has been used for decades and has become increasingly common across industry supply chains to cut costs and increase speed of delivery.
What has changed since the inception of cross-docking is the velocity of supply chains, degree of coordination and customer expectation for on-time-in-full (OTIF) orders.
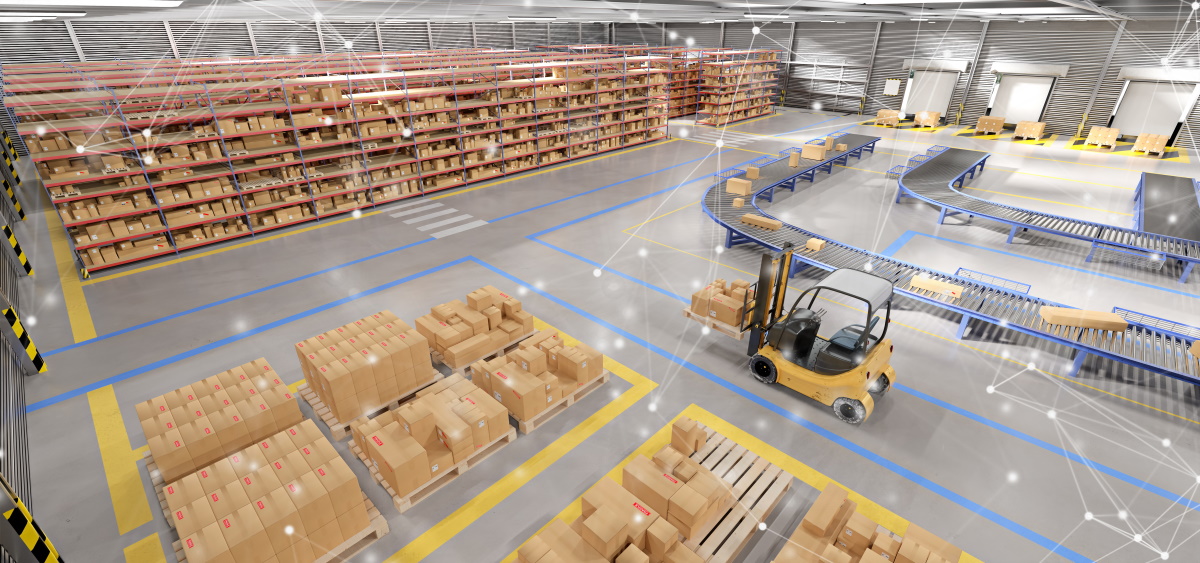
Cross-Docking Challenges and Solutions
To successfully implement and manage cross-docking, it is important to recognize some of the key challenges and associated solutions that go hand in hand with it.
Faster delivery expectations with a wider assortment of goods places more emphasis on the coordinated flow through the supply chain to deliver the perfect order.
Suppliers now are expected to deliver the perfect order in less time than ever before; in fact, in many instances, they are even expected to do so in 24 hours or less. Suppliers no longer have the luxury of housing all their products in a central or regional warehouse and shipping from there.
The efficiency of today’s supply chain depends on the ability (and agility) of companies to coordinate the movement of multiple items to a consolidation organization without inventory sitting at rest.
As an example, think of your local hardware store. To support in-store order fulfillment of everything from light fixtures to 2x4s on a 24-hour basis, the store must be able to not only locate items within the store, but at other store locations or suppliers, it must be able to ensure that items get on the right loading dock and to the store in plenty of time to ensure complete order readiness when customers arrive.
Even a single item misplaced along the way can be the difference between a repeat customer and one who takes his or her business elsewhere – in turn impacting the retailer-to-supplier relationship and associated profitability.
The increasing complexity of logistics networks means 3PLs are playing a greater role than ever before.
Large retailers and distributors are turning to specialist 3PLs and couriers to find the optimal combination and service to deliver a wider array of products. This makes managing a larger number of 3PLs to achieve a consistent level of service more complex and harder.
End-to-end visibility and control is harder as 3PLs have their own levels of sophistication and tracking systems. For the retailer or distributor, the burden falls on their own ability to track customer shipments and synchronize their timing for a unified order.
Paper-based inventory and order tracking leaves too much room for error.
There are four standard steps that define the journey of an individual item or order through the supply chain. As the breadth of products and carriers increases, tracking the flow of goods and paper become disconnected and leaving greater room for errors and muddying companies’ ability to identify, track and coordinate orders.
- Initial customer order: Comprised of countless SKUs and potentially hundreds or thousands of individual items by size, weight or number, the initial order must be made, logged and scheduled for delivery.
- Initial order fulfillment: Once scheduled, each order and its corresponding invoice must be loaded onto the appropriate truck or train at precisely the right time to make it to the next stop on schedule.
- Delivery: Let us assume that, in the case of our example order, each product made it to the hardware store on time and in good condition. Once at its final destination, the associated paperwork for each product in the order must accurately reflect delivery time and condition, then be returned to the appropriate office to be logged and duplicated as called for.
All items in the order then need to be brought together and given to the end consumer on schedule. At the same time, every part of the transaction must be well-documented in case of customer complaint or return.
With so many reams of paper to account for and so much room for human error along the way – invoices can be lost, orders incorrectly or incompletely logged, etc. – paper-based, manual tracking does not make cross-docking easy. Paper processes are a common source of problems that can ultimately degrade the customer experience.
While cross-docking may speed the delivery process, it also increases the potential for such errors in the inventory and tracking side of the equation. Even the notion of electronic documents such as PDFs are not sufficient for managing shipments.
To achieve true visibility and successful convergence of all the customer’s order, the data has to be shared in real-time and synchronized with a single view of the entirety of the order across the supply chain.
Automation is key to optimizing cross-docking and ensuring best-in-class supply chain and logistics practices.
Regardless of business size, location or product, every organization can benefit from an electronic proof of delivery system (ePOD) that connects companies, 3PLs and carriers to eliminate paper tracking and streamlines the overall delivery process.
Think, for example, of that same hardware store order. With multiple items coming from multiple locations, it would be easy for part of the order to be misplaced or damaged. In a paper-based system, the damage would have to be manually recorded and that recording sent back to be processed and it would be days before the issue would be identified and addressed.
In the case of a disagreement over the misplaced item, without a physical receipt marking proof of delivery, it would be the word of the recipient store against the delivery person that the item had arrived. ePOD, used via mobile apps, makes it possible for each shipment or order to be individually tracked throughout the chain of custody, with each stop noted and logged, recipient sign-off and any issues or comments captured electronically, and then submitted back through a common system.
During cross-docking, automation ensures that each item can be quickly scanned and moved to its next transport vehicle swiftly and accurately, logging any issues and noting special care instructions in each instance.
Beyond the cross-dock, the use of ePOD for end-to-end chain of custody tracking results in greater employee accountability, increased transparency for the originating supplier and provides end customers with an easy-to-navigate tracking site to check the status of an order and receive timely delivery and ETA notifications.
Conclusion
Cross-docking is a powerful concept to increase supply chain velocity, minimize inventory and offer a wider assortment of products to customers. However, these benefits come with a price – greater supply chain complexity and coordination.
Cross-docking solutions can address these challenges by automating the data flow across the supply chain and capture the movement of goods to ensure better coordination and visibility of exceptions as they occur to help ensure customers receive the perfect order every time.
Fleet Resource Center
Expand Your Routing, Mobile & Telematics Knowledge
Recommended For You


